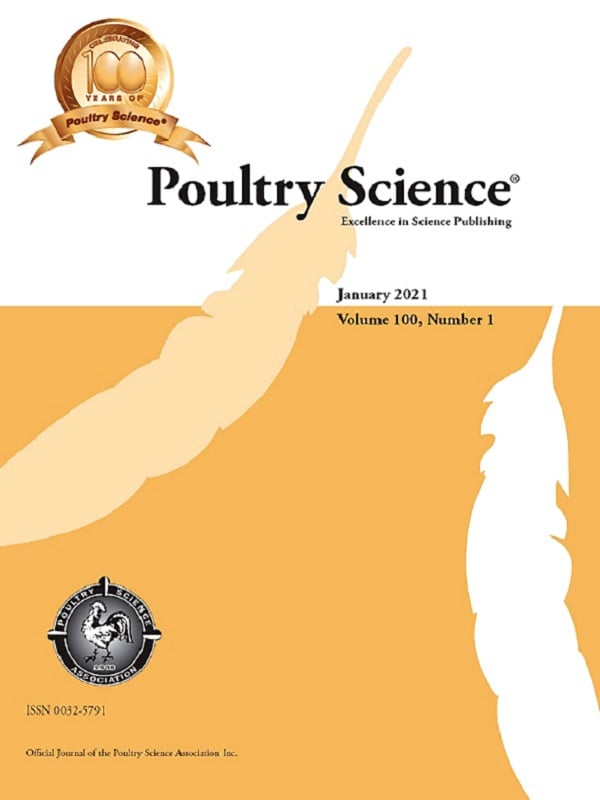
Effect of L-glutamic acid N,N-diacetic acid on the availability of dietary zinc in broiler chickens
- Poultry
The Poultry Research Facility has its own experimental feed plant, enabling us to produce all of the feed we use on location. This makes it possible to study a high variety of experimental diets and saves significant CO2-equivalent emissions from transport. All of the feed bags are precisely weighed before they are moved to the facility and colour coded to differentiate treatments.
The facility for laying hens can house over 1,500 hens and enables us to intensively monitor animal health and performance. Some pens are specifically designed to study the split-feeding concept, in which we provide a different feed composition to the laying hens in the morning and in the evening, to more precisely meet the nutrient requirements of hens during the egg formation cycle. This is a great example of sustainable precision nutrition, leading to better laying hen performance and reduced emissions of nitrogen and phosphorus into the environment. The laying hens’ facility enables us to fully control the environment and simulate different circumstances around the globe. We can study important animal measures such as feed and water intake, body weight and excreta composition, as well as shell and egg quality.
The hatchery allows us to monitor chicks right after hatching and study the effects of gender, genetics, fasting and immediate feed availability. This study is part of the LifeStart project, based on the philosophy that what happens during the first days of a chick’s life impacts its lifetime performance.
The broiler facilities can house over 6,000 birds, in a barn where the climate can be fully controlled. One of the studies performed in these facilities relates to our broiler model, which calculates feed costs, revenues and margin by predicting growth, FCR and carcass yield. Our feed additives portfolio has also been extensively studied at these facilities.
Our latest addition to the Poultry Research Facility, constructed in 2020, is a new climate-controlled poultry facility, with four identical research rooms that enable us to simulate contrasting environmental conditions and evaluate different solutions under either normal or more challenging scenarios. You can read more about this unit here.
This 124-pen facility can rear up to 37 animals per pen to market weights under controlled environmental conditions.
The 10,752 egg capacity hatchery unit allows us to test different early post-hatch feeding strategies.
This large meeting room is suitable for hosting up to 100 visitors, including scientists, producers and customers.
Different assays can be conducted in this lab. Raw materials and feeds can be analysed by NIR or wet chemistry, as well as faecal and intestinal samples. Egg, meat and bone composition and quality can also be determined.
The office is located on the research facility site. It provides a space for researchers, research technicians and the technical farm staff to convene to discuss the latest research findings and the technical side of the on-farm study execution.
This 2-room broiler unit with a total of 80 experimental pens (40 per room), can house a maximum of 47 animals per pen to market weights for nutritional studies. This barn also has four water tanks allowing us to test different water-delivered products.
This 2-room, sixty-four enriched cage facility (32 cages per room) allows us to rear up to 20 laying hens per cage in group housing. Each room can be individually environmentally controlled allowing for feed intake and egg production to be closely monitored under different production conditions.
Feed intake and egg production can be closely monitored for each individual hen, thanks to the two rooms that hold a total of 288 individual cages. The concept of split feeding was developed here.
The Poultry nutrition & health unit has four rooms with 48 pens each. The pens each have a maximum capacity of 22 animals at 42 days of age. The rooms are totally isolated, allowing us to test different challenges. Random water treatment distributions are also possible. The slaughter line facility allows us to assess impacts of nutritional interventions on commercially-relevant carcass quality traits (e.g. yield, meat myopathies), simulating a standard commercial slaughtering process with a capacity of 500 birds per hour.
All of the experimental feeds used in our studies is produced at the onsite feed plant (ISO 9001 certified). The experimental feed plant allows us to produce highly accurate feeds according to each study’s needs, due to intensive raw material control processes, and fully controlled automated dosing, mixing and pelleting processes.